Introduction
CW 4 Parts Manufacturer, also known as Copper Alloy CW 4, are vital components in various industries due to their excellent mechanical properties and durability. These parts are manufactured using a specific copper alloy composition, which makes them suitable for a range of applications where strength, corrosion resistance, and machinability are essential. In this guide, we will explore what CW 4 parts are, their benefits, typical applications, and how to choose the right CW 4 Parts Manufacturer for your needs.
Composition of CW 4 Alloy
The exact composition of CW 4 alloy can vary, but it typically includes:
- Copper (Cu): The primary element, providing high thermal and electrical conductivity.
- Zinc (Zn): Added to improve strength and hardness.
- Tin (Sn): Enhances corrosion resistance and overall durability.
- Lead (Pb): Improves machinability and lubrication during processing.
Advantages of CW 4 Parts
Excellent Machinability: The addition of lead in the alloy composition ensures that CW 4 can be easily machined to precise specifications, reducing production time and costs.
High Strength: The combination of copper with zinc and tin provides high tensile strength, making CW 4 suitable for load-bearing applications.
Corrosion Resistance: Tin enhances the alloy’s resistance to corrosion, making CW 4 ideal for use in environments where they are exposed to moisture or chemicals.
Thermal and Electrical Conductivity: Copper’s inherent properties ensure that CW 4 have excellent thermal and electrical conductivity, essential for electronic and electrical applications.
Durability: The robust composition of the CW 4 alloy results in parts that are long-lasting and capable of withstanding harsh conditions.
Applications of CW 4 Parts
Automotive Industry: Used in various engine components, fittings, and connectors due to their strength and resistance to wear and tear.
Electrical and Electronics: Essential for connectors, terminals, and other components where electrical conductivity is crucial.
Marine Applications: Ideal for use in marine environments due to their superior corrosion resistance.
Plumbing and HVAC: Commonly used in fittings and valves that require reliable performance and resistance to corrosion.
Machinery and Equipment: Utilized in the manufacturing of durable parts that can withstand high stress and harsh operating conditions.
Choosing the Right CW 4 Parts
When selecting CW 4 for your application, consider the following factors:
Application Requirements: Determine the specific needs of your application, including load-bearing capacity, environmental exposure, and thermal or electrical conductivity requirements.
Quality Standards: Ensure that the CW 4 meet relevant industry standards and certifications for quality and performance.
Supplier Reputation: Source parts from reputable suppliers known for their high-quality products and reliable service.
Customization Needs: Consider if you need custom parts manufactured to specific dimensions or specifications. Many suppliers offer customization services to meet unique project requirements.
Maintenance and Care for CW 4 Parts
To maximize the lifespan and performance of CW 4, regular maintenance and proper care are essential. Here are some tips:
Regular Inspection: Periodically inspect CW 4 for signs of wear, corrosion, or damage.
Cleaning: Clean parts using appropriate solvents and methods to remove dirt, grease, and other contaminants. Avoid using abrasive cleaners that can scratch or damage the surface.
Protective Coatings: Apply protective coatings or lubricants to parts exposed to harsh environments to enhance their corrosion resistance and longevity.
CW 4 Parts Manufacturer FAQs:
What are CW 4 parts made of?
CW 4 parts are made from a specific copper alloy that typically includes copper, zinc, tin, and lead. This combination enhances the alloy’s strength, machinability, and corrosion resistance.
Can CW 4 parts be customized?
Yes, many suppliers offer customization services for CW 4 parts. This allows you to get parts manufactured to specific dimensions or specifications that meet your unique project requirements.
Are CW 4 Parts Manufacturer suitable for high-temperature applications?
CW 4 parts can handle a range of temperatures, but it’s essential to verify their suitability for high-temperature applications with your supplier. The alloy’s properties provide good thermal conductivity and durability.
How do CW 4 Parts Manufacturer compare to other copper alloys?
CW 4 Parts Manufacturer offer a balance of machinability, strength, and corrosion resistance that makes them versatile and reliable. While other copper alloys may excel in specific areas, CW 4 Parts Manufacturer provides a well-rounded option for a variety of applications.
Conclusion
CW 4 Parts Manufacturer offer a blend of strength, durability, and excellent machinability, making them indispensable in various industries. Their unique properties make them ideal for applications where reliability and performance are paramount. By understanding the benefits, applications, and selection criteria for CW 4 parts, you can make informed decisions that ensure the success and longevity of your projects.
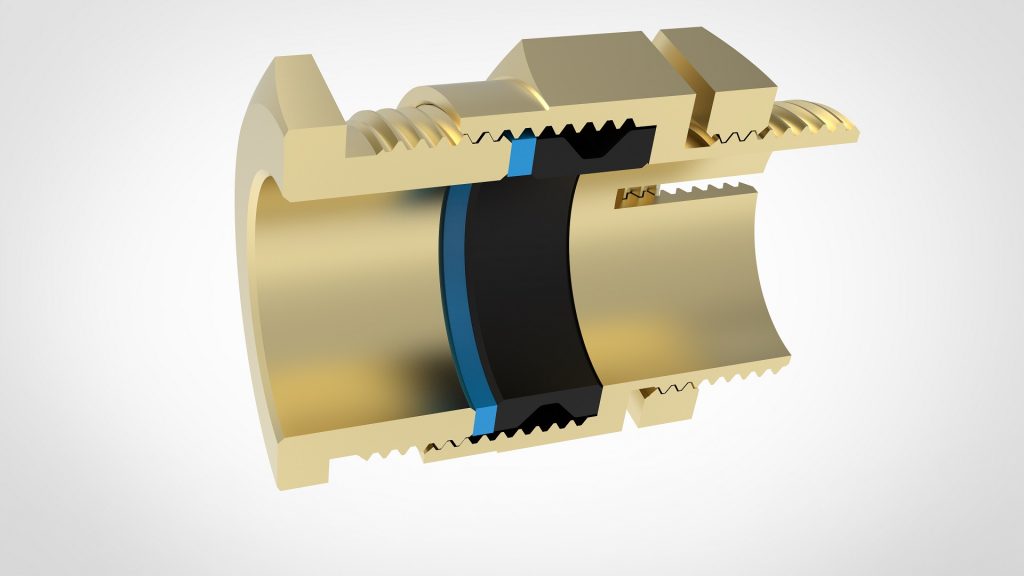